Activity Based Costing Drivers Examples
In this example, the wages expense actually gets used in an activity called serving or serving customers. Note that the process of serving a regular hot dog customer requires two steps, but the process of serving a chili dog customer actually requires five steps. These steps are known as cost drivers. What is Activity Based Costing? Activity based costing (also known as ABC costing) refers to the allocation of cost (charges and expenses) to different heads or activities or divisions according to their actual use or on account of some basis for allocation i.e. (cost driver rate which is calculated by total cost divided by total no. Of activities) to arrive at a profit.
Activity-based costing and management
Suppose you go to a movie theater that has five screens showing five different movies. Jerome Justin works for the movie theater selling tickets for all five movies. Suppose management wants to know the cost of selling tickets per movie and asks you to assign Justin’s wages to each of the five movies. How would you assign his wages?
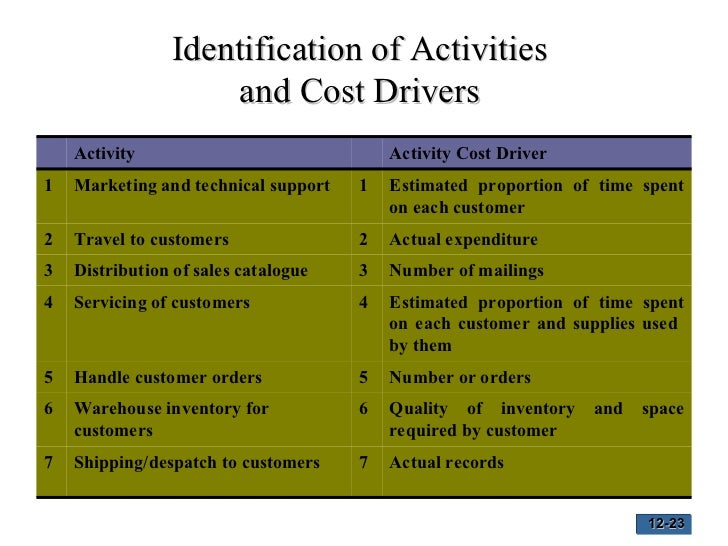
You could simply divide Justin’s wages by the number of movies and allocate 20% (1/5 = 20%) of his salary to each movie. Or you could figure out how many tickets he sold to each movie, and allocate his wages on the basis of ticket sales. For example, if 50% of the ticket sales were for Avatar, you might allocate 50% of Justin’s wages to Avatar. You probably also could think of additional ways to allocate Justin’s wages. No matter how we allocate Justin’s wages, his wages would not be directly traceable to one of the movies if he sold tickets for all five movies. In short, the allocation of Justin’s wages to a particular movie is at least somewhat arbitrary because alternative methods could allocate different amounts of Justin’s wages to each movie. Justin’s wages would be indirect costs to the different movies because his wages could not be directly assigned to any one of the movies.
By definition, the allocation of indirect costs is at least somewhat arbitrary. Nevertheless, accountants have discovered that they can improve the ways costs are assigned, such as to movies in this case, by using activity-based costing.
Activity-based costingis a costing method that assigns indirect costs to activities and to the products based on each product’s use of activities. Activity-based costing is based on the premise: Products consume activities; activities consume resources.
Activity-based costing identifies the activities generating costs and assigns costs to those activities. Take the earlier Justin example. By focusing on Justin’s activities, management could learn what caused costs and find ways to improve Justin’s efficiency. Suppose that by studying Justin’s activities, management learns he spends 40% of his time answering questions about movies, 40% of his time selling tickets, and 20% doing nothing. Based on this information, management could think about better ways to use Justin’s time. By improving their signs and posting information about the movies, management could reassign Justin to other tasks.
Closely related to activity-based costing is the notion of activity-based management (ABM). Using activity-based management, managers identify which activities consume resources. The focus is then to effectively manage costly activities with the goal of reducing costs and improving quality. Consider Justin and the movie theater again. Using activity-based management, managers would identify what Justin did with his time and perhaps find ways to help him become more efficient.
Let’s look at a company that makes clothing. The product does not cost less under one system or another. Our problem is that no cost system measures costs perfectly. We are able to trace some costs directly to the product. For example, we are pretty accurate in measuring the cost of denim, which is a direct material, in each of our shirts, pants, jackets, and so forth.
Activity-based costing and management
Suppose you go to a movie theater that has five screens showing five different movies. Jerome Justin works for the movie theater selling tickets for all five movies. Suppose management wants to know the cost of selling tickets per movie and asks you to assign Justin’s wages to each of the five movies. How would you assign his wages?
You could simply divide Justin’s wages by the number of movies and allocate 20 per cent of his salary to each movie. Or you could figure out how many tickets he sold to each movie, and allocate his wages on the basis of ticket sales. For example, if 50 per cent ofthe ticket sales were for Avatar, you might allocate 50 per cent of Justin’s wages to Avatar. You probably also could think of additional ways to allocate Justin’s wages. No matter how we allocate Justin’s wages, his wages would not be directly traceable to one of the movies if he sold tickets for all five movies. In short, the allocation of Justin’s wages to a particular movie is at least somewhat arbitrary because alternative methods could allocate different amounts of Justin’s wages to each movie. Justin’s wages would be indirect costs to the different movies because his wages could not be directly assigned to any one of the movies.
By definition, the allocation of indirect costs is at least somewhat arbitrary. Nevertheless, accountants have discovered that they can improve the ways costs are assigned, such as to movies in this case, by using activity-based costing.
Activity-based costingis a costing method that assigns indirect costs to activities and to the products based on each product’s use of activities. Activity-based costing is based on the premise: Products consume activities; activities consume resources.
Numerous companies, such as HP, Caterpillar, and IBM, have implemented activity-based costing. Activity-based costing (ABC) has revealed startling information in these companies. For example, after installing new costing methods, one well-known company found that one of its products, a printed circuit board, was generating negative margins of 46 per cent.
Activity-based costing identifies the activities generating costs and assigns costs to those activities. Take the earlier Justin example. By focusing on Justin’s activities, management could learn what caused costs and find ways to improve Justin’s efficiency. Suppose that by studying Justin’s activities, management learns he spends 40 per cent of his time answering questions about movies, 40 per cent of his time selling tickets, and 20 per cent doing nothing. Based on this information, management could think about better ways to use Justin’s time. By improving their signs and posting information about the movies, management could reassign Justin to other tasks.
Closely related to activity-based costing is the notion of activity-based management (ABM). Using activity-based management, managers identify which activities consume resources. The focus is then to effectively manage costly activities with the goal of reducing costs and improving quality. Consider Justin and the movie theater again. Using activity-based management, managers would identify what Justin did with his time and perhaps find ways to help him become more efficient.
Let’s illustrate by looking at a textile company that makes jeans. We will use this company as a basis to demonstrates important issues about the difficulty with traditional cost allocation methods and the advantages of activity-based costing.
The product does not cost less under one system or another. Our problem is that no cost system measures costs perfectly. We are able to trace some costs directly to the product. For example, we are pretty accurate in measuring the cost of denim, which is a direct material, in each of our shirts, pants, jackets, and so forth.
Overhead costs are another matter. Overhead includes costs like electricity to run machines and salaries of product designers and inspectors. All these costs are allocated to products. We know quality control inspectors cost money, but we do not know how much of that cost is caused by a particular jacket or pair of pants. So we make some assumptions about the relation between products and overhead costs. For example, we typically allocate overhead based on machine-hours required to stitch and fasten snaps. While that is probably a reasonable way to allocate the costs of electricity to run machines, its not a desirable way to allocate the cost of quality control inspectors.
overhead allocation is somewhat arbitrary (it is based on an estimate only), how will activity-based costing help?
Activity-based costing provides more accurate information because we can identify which activities cause costs, and we can determine the cost of the activity. Activity-based costing identifies and measures the costs of performing the activities that go into a product much better than traditional cost methods. For example, if a particular jacket requires 10 inspections for a production run of 1,000 jackets, we figure out the cost of those inspections and assign that cost to the production run for this particular jacket.
This page covers 3 element Yagi Antenna calculator.The formula and basics of Yagi Antenna Calculator are also explained with example.The calculators for other antenna types such as parabolic,horn,dipole and patch are also mentioned. Free Online Engineering Calculator to find the Dimensions of a yagi Uda Antenna for a given Frequency Range and Length. Yagi Uda Antenna Calculator You may want to combine it with a folded Dipole. With this Yagi antenna calculator, you will be able to build your own yagi antenna or at the very least compare it to other commercially made yagi antennas. Another ham brought to my attention, that I should have indicated if this yagi antenna calculator is built with the Yagi beam elements isolated from the boom or not isolated.
But exactly how would activity-based costing help us cut production costs?
Once we identify activities that cause costs, we can eliminate or modify costly activities. For example, if we find that a jacket requires too many costly inspections, we could redesign the jacket to reduce the need for inspections. Our current cost system allocates all overhead costs, including inspection costs, to products based on machine-hours. We really do not know how much it costs to make an inspection and how much inspection cost is required by each product.
Because activity-based costing provides more information, it takes more time than traditional cost systems. New accounting methods sound great in theory, but there must be enough benefit from improved management decisions to justify the additional work required to provide numbers.
Key points about activity-based costing:
- The allocation of indirect costs is at least somewhat arbitrary, even using sophisticated accounting methods.
- Activity-based costing provides more detailed measures of costs than traditional allocation methods.
- Activity-based costing can help marketing people by providing more accurate product cost numbers for decisions about pricing and which unprofitable products the company should eliminate.
- Production also benefits because activity-based costing provides better information about the cost of each activity. In practice, ABC helps managers identify cost-causing activities. To manage costs, production managers learn to manage the activities that cause costs.
- Activity-based costing provides more information about product costs than traditional methods but requires more record-keeping. Managers must decide whether the benefits or improved decisions justify the additional record-keeping cost.
- Installing activity-based costing requires teamwork among accountants, production managers, marketing managers, and other nonaccounting people.
Next, we discuss the methods used for activity-based costing and illustrate them with an example.
See Also:
Cost Center
Value Drivers: Building Reliable Systems to Sustain Growth
Direct Labor Variance Formulas
Direct Material Variance Formulas
Step Method Allocation
In accounting, the cost driver definition is a factor that incurs cost. Use cost drivers to allocate variable and indirectcosts to production activities or output. Include both indirect costs and direct costs to compute the full cost of production. Because indirect costs, such as variable overhead, are not directly traceable to production activities, allocate them according to a cost driver rate to apply these costs to production activities. Based on the activity of the cost driver, the cost driver rate is the rate indirect costs applied to production activities.
Download the free Know Your Economics guide to easily manage the factors incurring costs in your company.
Choosing Cost Drivers
An indirect or variable cost may have several possible cost drivers. Traditional costing methods allocate indirect costs to production activities based on volume of output. Conversely, activity-based costing allocates indirect costs to particular production activities related to that cost.
When deciding which driver to use in terms of allocating indirect cost, consider the cause-and-effect relation between the cost and the driver. In addition, consider whether or not the cost driver activity is easily measurable. It is also necessary to consider the cost behavior of the relevant cost. The relevant cost refers to the cost’s response to the activity of the driver. In addition, approximate the relationship between costs and cost drivers using regression analysis.
Use these drivers at differing hierarchical levels. For example, an indirect or variable cost may be relevant at the unit level, the batch level, the product level, the customer level, or the facility level. Once you determine the appropriate hierarchical level, choose a cost driver activity at that level in order to allocate the indirect or variable cost.
Cost Driver Rates
A cost driver rate is the amount of indirect or variable cost assigned to each unit of cost driver activity. For example, you may apply indirect overhead to direct labor hours as $50 dollars per hour. In this case, for each hour of direct labor required for production, the company would then allocate $50 of indirect overheadcosts to the production activities or output.
Cost Driver Examples
For illustrative purposes, below are some cost driver examples of indirect or variable costs as well as relevant cost driver bases for these costs.
If you want to check if your unit economics are sound, then download your free guide here.
Strategic CFO Lab Member ExtraAccess your Projections Execution Plan in SCFO Lab. The step-by-step plan to get ahead of your cash flow.
Click here to access your Execution Plan. Not a Lab Member?
Click hereto learn more about SCFO Labs
Source:
Hilton, Ronald W., Michael W. Maher, Frank H. Selto. “Cost Management Strategies for Business Decision”, Mcgraw-Hill Irwin, New York, NY, 2008.